トヨタ流問題解決というと、「A3仕事術」が有名で、「問題の明確化〜対策実施、標準化」
までを8ステップに分けて実施し、それをA3の用紙1枚にまとめるのが特徴です。
今回は、その8ステップについて、今まで誰も教えていない極意をお伝えします。
1. 問題解決とは?
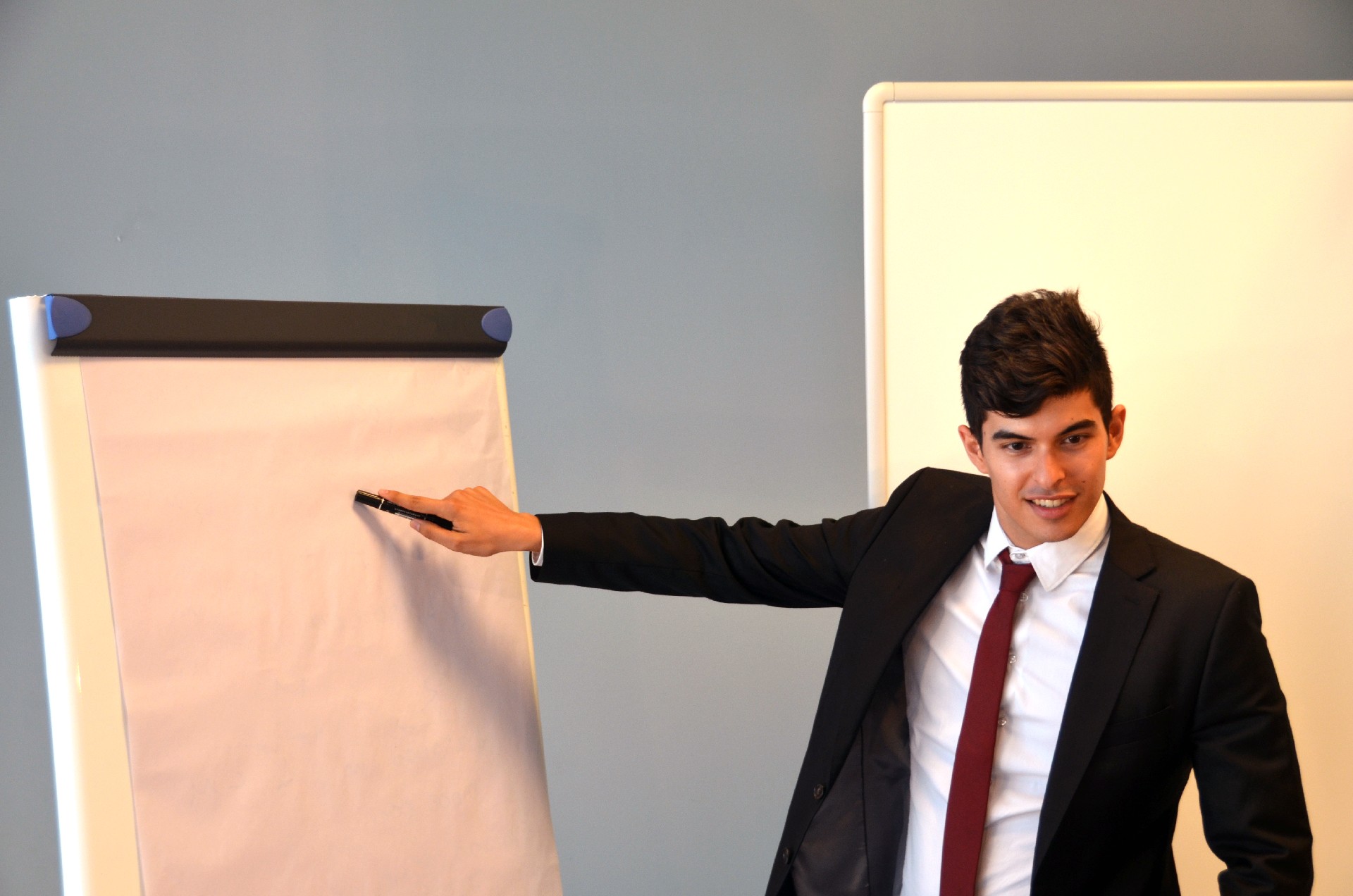
トヨタ流問題解決とは?
私たちは仕事の中で、あるいは社会生活の中で、ありとあらゆる問題に直面します。
ここで、問題とは、実現したい状態、あるいは、ありたい姿と現状のとのギャップと
定義します。
そのギャップがなぜ発生しているのかを探り、問題点として認識し、その問題点を
解消するための克服すべき課題を特定し、対策案を立案して実行し、評価・標準化
と進むのが大きな問題解決の流れです。
したがって、問題解決とは仕事の仕方の中心となるスキルであり、考え方です。
問題解決なくして成り立つ仕事はないと言っても過言ではないでしょう。
しかし、それほど重要なスキルであるにもかかわらず、実際に運用するにあたって
誰もが間違いやすい部分の詳細な解説がほとんどなされておらず、中には
明らかに間違った解説すら存在するのが実情です。
今回はそういった部分も含めて、誰にもわかりやすく解説します。
2. 問題解決の8ステップとは?
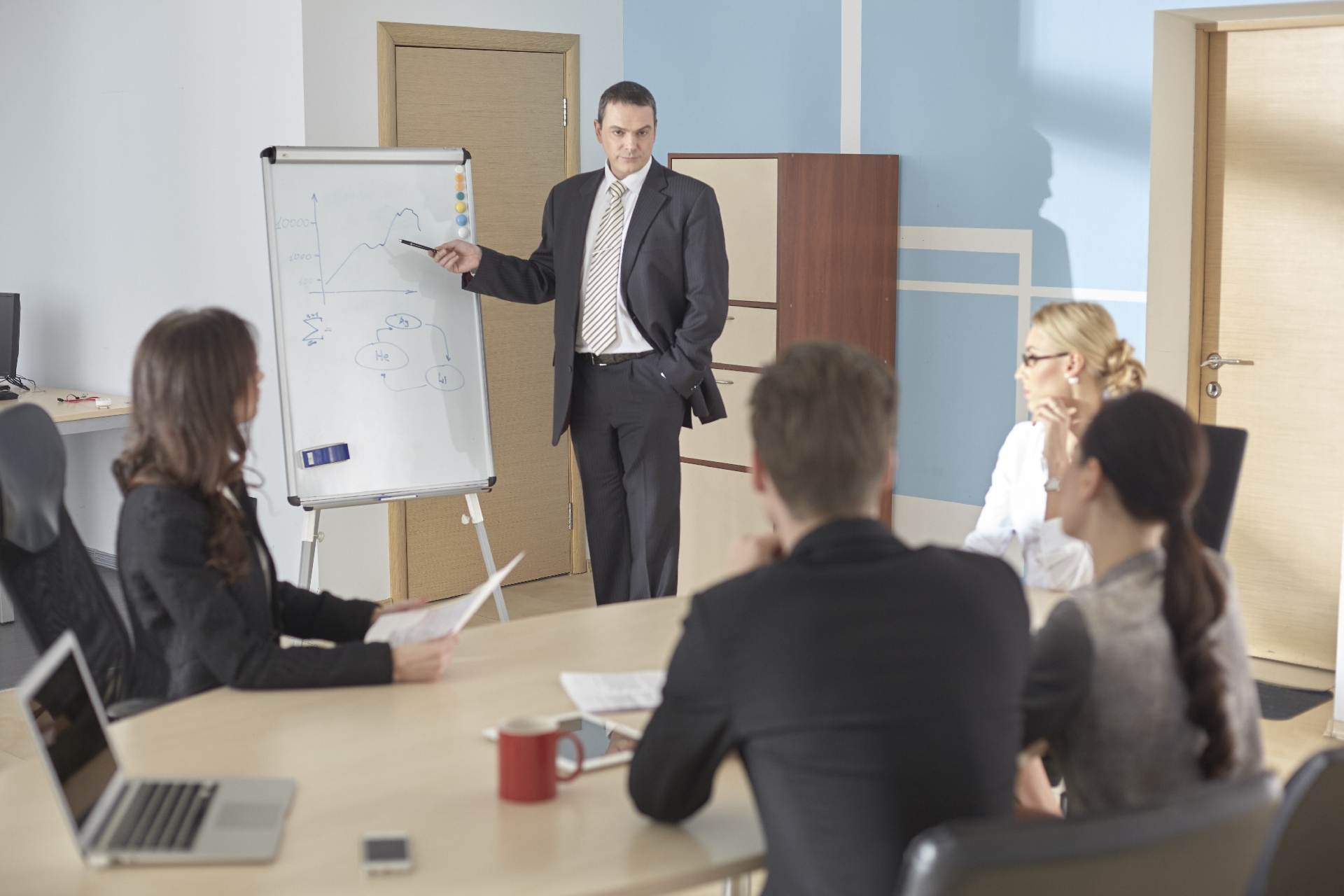
問題解決の8ステップ
トヨタ流問題解決というと、「A3仕事術」が有名なのですが、
それはこれから解説する8ステップをA3用紙1枚にまとめたものです。
「A3仕事術」の詳細についてはこちらの記事もご覧ください。
「トヨタ流問題解決「A3仕事術」の誰も知らない本当の狙い」
それではトヨタ流問題解決の8ステップについて解説をしていきます。
まず最初に、問題解決の8ステップを図1に示します。
図1.問題解決の8ステップ
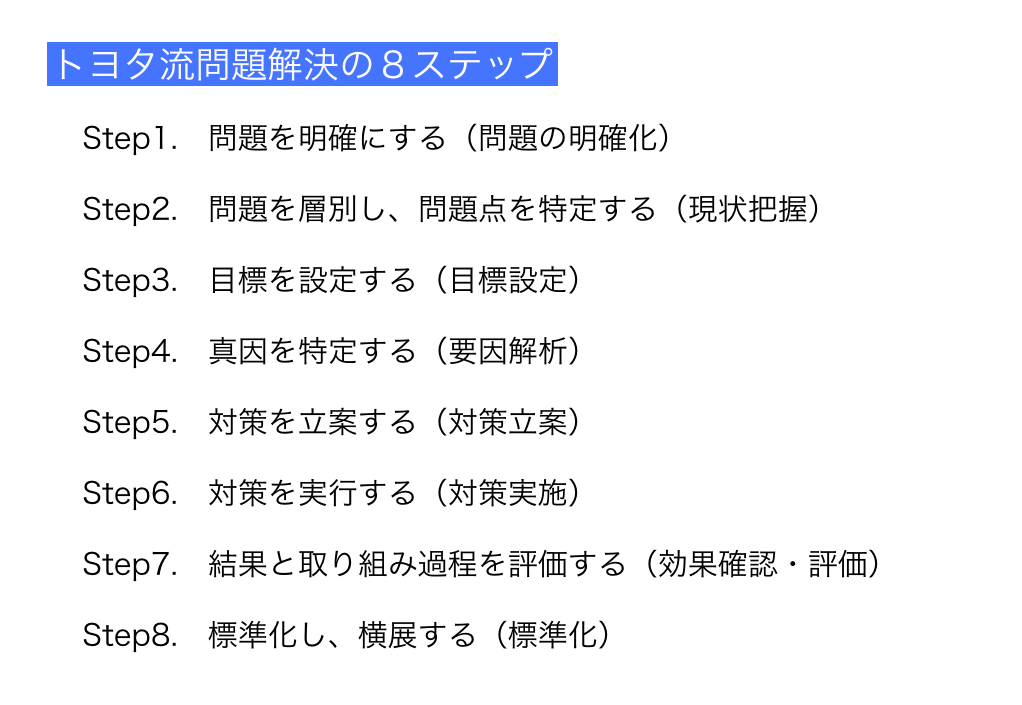
問題解決の8ステップ
以下、それぞれのステップにおける重要な点を詳しく解説します。
(1)ステップ1:問題の明確化
まず最初にするのは「問題とは何か」という問題の定義づけです。
「問題とはあるべき姿と現状とのギャップである」
図2に問題の定義づけを示します。
図2.問題の定義づけ
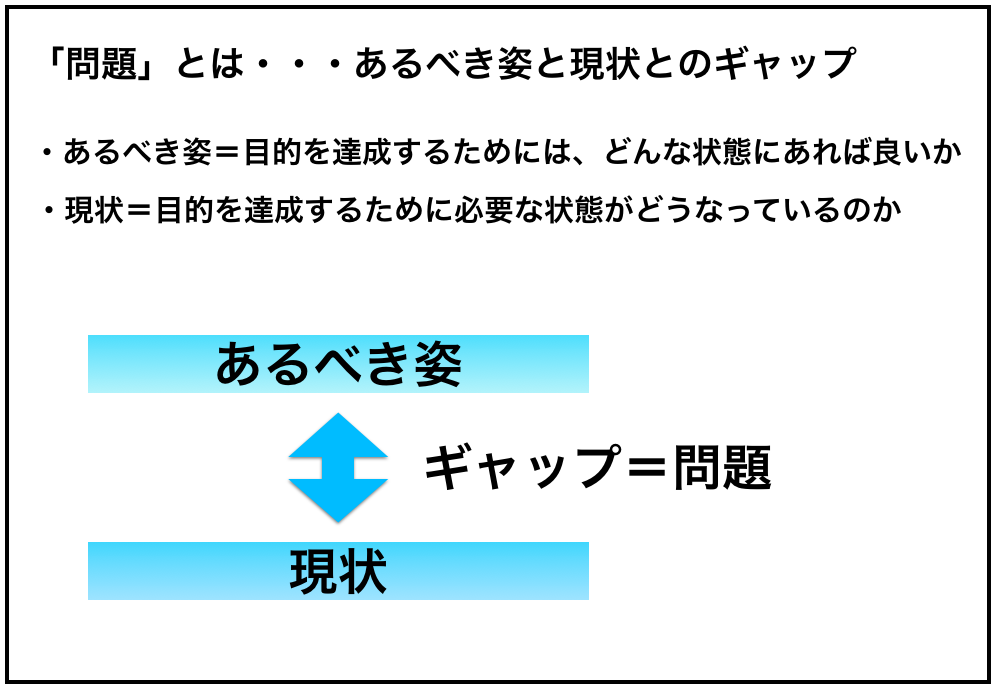
問題の定義づけ
ここで十分注意しなければならないことがあります。
それは、「あるべき姿は現象で表現してはいけない」ということです。
たとえば、実現したい姿が「品質不具合ゼロ」だとします。
すると、あるべき姿も「品質不具合ゼロ」としてしまいがちです。
対して、現状は「品質不具合5件」であるならば、問題はあるべき姿と現状
とのギャップなので、問題は「品質不具合5件」となってしまいます。
これでは、現状と問題が同一となってしまって、思考が1ミリも深まっていません。
したがって、このステップが何の進展もない無駄なステップになってしまいます。
それでは、どう考えるべきなのでしょうか。
それは、あるべき姿は実現したい姿を成立させる条件として考えるのです。
その例を図3に示します。
図3.あるべき姿から問題を導き出す
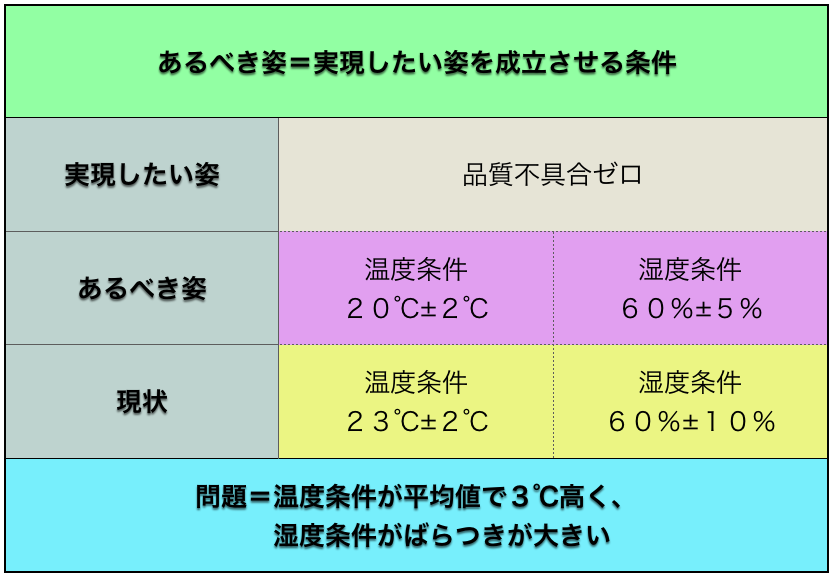
あるべき姿から問題を導き出す
このように考えれば、実現したい姿から、それを成立させる条件をあるべき姿とし、
その条件が現状ではどうなっているのかを調べれば、無理なく問題を定義する
ことができます。
ここまで整理できれば、問題がよりはっきりし、以下のステップがスムーズに進められます。
(2)ステップ2:現状把握
ステップ1で問題の定義づけができているので、この場合の現状把握は
ステップ1の例で考えると、
・温度条件について
平均値が3℃高くなるようなことに関連するようなことが何かあるかどうか
現状の設定条件、機器の作動状態などを現地現物で詳しく調べます。
たとえば
1日の中で時間帯によって温度が徐々に変化する
周囲の温度が高くなると設定温度から外れて高くなる
ランダムに設定温度から外れる 、など
・湿度条件について
ばらつきが2倍くらいに大きくなるようなことに関連することが何かあるかどうか
調湿機能のばらつきの大きさ、センサーの異常、外部との密閉状態などに異常
がないかなど、現地現物で詳しく調べます。
たとえば
加湿開始時に設定を大きく外れてから徐々に収斂していく
温度が高くなると、湿度が低く外れる
次に、今調べた現状とステップ1で問題とした条件との関係を調べます。
たとえば
温度条件について
時間帯✖︎実測温度の推移、周囲温度✖︎実測温度
湿度条件について
加湿開始から設定湿度までの時間別湿度推移、温度✖︎湿度
というように、現状把握ではあるべき姿を実現できていない要因系と思われる
ようなことに関連していそうな事柄を詳しく調べます。
これによって、問題を引き起こしている要因系が明確になってきます。
ここで、問題を引き起こしている原因が問題点となります。
たとえば、
温度条件について
周囲温度の影響を受けていることが明らかであり、遮熱性能不足が問題点です。
湿度条件について
加湿開始から収斂するまでにオーバーシュートして設定範囲を超えてしまうことが
明らかであり、加湿弁の制御方式が追随できていないことが問題点です。
というように、問題点が具体的に浮き彫りになります。
さらに、その問題点を解消するために克服すべき内容を考えると
たとえば
温度条件について
断熱材の材質と厚みを適正化する
湿度条件について
測定値に近づいたら徐々に加湿弁の開度調整が可能な制御方式に変更する
というように、ステップ1で問題を明確化した後、ステップ2では現状把握をし、
問題点と課題を明確にすることができます。
(3)ステップ3:目標設定
目標を決める時に最も重要なことは、目的に立ち返って、目的を満足できる
目標を設定することです。
目標に具備すべき要件は、「いつまでに、何を、どのレベルにする」ということです。
たとえば、ステップ2では課題が明確になっているので、
・温度条件について
・湿度条件について
また、目標設定の時に起こしやすい間違いとして次のものがあるので
注意が必要です。
①「実現したい姿」を目標にしてしまう
たとえば、目標を「品質不具合ゼロ」としてしまうと、これまで問題、問題点、課題
というようにブレークダウンしてきたものが無駄になり、元に戻ってしまいます。
これが堂々巡りに陥る典型的なパターンです。
(せっかくブレークダウンしたものを元に戻してしまうので当たり前)
目標はあくまでも課題を克服するためのものでなくてはなりません。
②「対策」を目標にしてしまう
対策は課題を克服するための手段です。手段と目的を混同してはいけません。
(4)ステップ4:要因解析
要因解析は原因と結果との関係を明らかにすることです。
ここで、私たちが実施したいことは、失敗の経験から、システムの不備、脆弱性を認識し、
同様の問題を起こす可能性を低くするための組織的活動へ結びつけることです。
そのためには、起きた問題の発生構造の全体を知り、現実的な対策を講じて類似の
問題の再発防止、未然防止を実現することを通じて、組織のマネジメントレベルを
あげる組織的な活動に繋げたいのです。
その時に考慮すべき要素が4つあります。
第一は「技術」です。
望む結果を得るための固有技術(目的達成のための再現可能な方法論)が確立
しているのかどうかということです。もしも、問題の原因がここにあるのなら、技術
的資産(技術標準、マニュアルなど)の根拠と妥当性を見直しして、不足、不備
を解消する必要があります。
第二は「マネジメント」です。
技術的にどうすればよいかわかっていても、日常業務の中で、実行できる手順、
マニュアル、業務環境、業務支援などが適切に準備されていることが必要です。
特別に訓練された人でなく、普通の人が実施可能な実施手順の確立と運用が
必要なのです。
第三は「ひと」です。
目的達成のための再現可能な方法論としての技術が確立していて、その技術を
組織的に活用して目的を達成するためのマネジメントの仕組みがあっても、その
もとで業務を実施するひとに能力と意欲がなければ、期待通りには実施されません。
そのためには、知識、技術、技能の訓練と理解が必要であり、人々の主体的な
参加を促す仕組みやヒューマンエラーを防止、監視する業務システム、組織運営
になっているかどうかが重要で、この部分に問題がないのかという検討も必要と
なります。
第四は「組織風土・文化、価値観」です。
技術が確立し、技術を活かす健全なマネジメントが運用され、良い人々がいても、
すべての業務がそれらの規範だけで行われるわけではなく、時には、安きに流れ
たくなる誘惑の中で実施しなければならないこともあり、そのような時に、業務遂行
に関わる健全な価値観が浸透していて、組織の風土・文化が盤石であると間違い
が起こりにくいのです。その部分の改善の余地がないかどうかを検討することも
重要です。
何か問題が起こった時に、私たちがまず最初にしたいことは不具合事象や問題事象
に対する処置です。
この場合は、進行中の問題に対する対応となるため、早期に解消することが重要です。
こうしたケースでは、現地現物で事実を確認しながら進める「なぜなぜ分析」が有効に
なることがあります。
しかし、原因の除去が素早くできれば良いのですが、そうでなくてもとにかく問題事象の
影響を極小化することが求められます。
①「なぜこの現象が起こるのか:現象の連鎖をよく観察する」
「現場観察」 ・・・ 現地、現物、現実に基づく
まずは現地に出向き、現物を前にして、そこで起こっている現実を正しく認識することが
最も重要です。そして、その現実を丁寧に観察します。ここで大事なことは、問題事象を
引き起こしている原因系を目で見て確認することです。
ここでは、目の前で起きている問題事象に至るまでの、現象の連鎖を明らかにできるまで、
現場で粘り強く丁寧に観察します。
「最初にこの現象が起きて」→「次にこの現象が起きて」→「結局、この問題事象となる」
②「なぜこのような現象が物理的に成り立つのか」
「物理的にとらえる」→目の前で起きている現象を物理的に説明する
「〇〇が△△となって××という現象になる」というような簡単な文章で成り立つ理屈を
表現します。
③「どの要素とどの要素がどう関係するとなぜこの現象になるのか」
「発生メカニズムを考える」 ・・・ 構成する2つ以上の要素のお互いに関係を明確にする
「〇〇が△△となって××という現象になる」というようなことが実際に起こるメカニズム
を推定します。
この時、メカニズムは複数想定されるケースが多く、実際の現場の発生状況から
推定メカニズムを絞り込むことが重要となります。
④「なぜこの不具合発生メカニズムが成立するのか」
「原理・原則を考える」 ・・・ 不具合発生メカニズムが成立する条件を探す
不具合発生メカニズムを原理・原則に当てはめて理解します。
問題事象が物理事象として起こっているのなら、必ず何らかの物理法則に従っている
ので、その物理法則が成立する条件を明確にします。
不具合発生は正常な状態からの逸脱なので、正常な状態との条件の差が生じる理由
を探します。そこから、不具合発生の成立条件が明らかになります。
⑤「その成立条件を阻害できる条件を考える」
「どこで影響を断ち切ることが有効かを考える」 ・・・ 結果への影響を防止する
問題事象が起こる条件を突き止められたら、どこでその成立する条件を阻害できれば
結果への影響を断ち切れるかが重要です。
複数案の中から、最も早く、安く、効果的に実行できる案を選択し、効果確認後、
標準化します。
このように、素早く的確に、起きている問題を収束させることが重要です。
ここで、原因と要因の意味の違いについて整理しておきたいと思います。
要因:ある事象に影響する(ある事象を起こしうる)もの
原因:今回その事象を起こしたもの
私たちが実施したいのは、数ある要因の中から、今起きている問題事象の原因を
突き止め、素早く的確に対応し、収束させることなのです。
原因を突き止めるためには、いろいろな手段がありますが、いずれの場合も、
問題を起こしている「状況」の把握を重視すべきです。
たとえば、「ある設計者がうっかりミスをした」という例について考えると
①この人がミスをしたという設計中に、何を設計しなければならないかわかっていたか
②うっかり重要なことを考慮できなかったとすると、考慮すべき事項が何であると考えて
いたか、どのような観点からそれを考慮すべきと考えていたか
③ある特定の技術分野の知識が不足しているとしたら、どのような側面の知識について
弱いのか、それらの知識を総動員できる開発インフラや開発プロセスがあったのか
などについて詳しく確認すべきです。
このように、物理的、あるいは、化学的な現象以外の業務プロセス上の問題などに
ついては、安易に「なぜなぜ分析」に拘泥し、皮相的な意味での「なぜなぜ問答」を
したところで問題は解決せず、現実的な対応策には行き着けません。
〇〇ミス→考慮不足→危ないと思わなかった→注意不足→ぼっとしていた→寝不足
→睡眠時間確保
このような例には事欠きません。必ずしも間違いではないかもしれませんが、いかにも
的外れであることは明らかでしょう。
そこで、こうしたケースでは私たちは次の手順で進めたいと考えています。
【手順1】状況把握
1)問題の実態を把握する
現地・現物で事実を観察することが重要(事実と意見・見解・憶測との峻別)
2)事象の連鎖の理解
何が起きて、それに誘導されて次に何が起きたのかという連鎖を明らかにする
(理由・原因についてはあまり深く考えず、次に解明する問題の構造に関係しそうな
事実を把握するよう努める)
・人がどんな状況で何を考え、どういう意図で何をしたか(人の思考・行動プロセス)
・問題が物理・化学的な現象に関わるなら、目で見た観察結果や科学的な測定・
分析の結果を聞く
・比較:通常はどうやっている、類似のものとどこが違う
・変化:いつから何が変わったか、時間の経過とともに変わっている何かがあって
それが直接・間接の原因になっていることがある
・関係者分析:どのような関係者がいて、誰が誰に何をすることになっているか
3)問題の領域の明確化
どのプロセスで問題が起きているか、どの機能(ニーズ、実現構想、実施、検証、
提供など)の問題なのか、どの部門(あるいは人)の間の関係の問題なのか
【手順2】原因構造解明
問題が起きたその因果構造の全貌を明らかにする
1)問題が、その分野に固有の技術・知識の未熟さに由来するものかどうか
・技術が未熟な場合:組織の技術資産、知識レベルの充実を図る必要がある
・確立している技術・知識が組織共有のものとして有効活用されていない場合
→マネジメントシステムの改善が必要(ほとんどこのケース)
2)マネジメントの改善が必要かどうか
・計画の問題か、実施の問題か
・業務プロセスの中にどのプロセスで見逃し、どのプロセスで拡大させたのか
・業務を実施する「ひと」に十分な能力や意欲があったのか
・正しい業務を遂行できる健全な価値観、組織の風土・文化、しつけが浸透しているか
【手順3】対応検討
将来起きるかもしれない問題にどう対応するか
1)どの因果連鎖をどう断ち切るか
・効果、経済性、(技術的)実現可能性、対応策実施の完全性・継続性、副次的効果
・できないこと、する気のないこと、守れないこと、実施しても効果の小さいこと、
副作用の大きいことは実施すべきではない
(5)ステップ5:対策立案
対策立案にあたって、まず考えることは問題事象に関して、原因からの影響をどこで
どう断ち切ることが効果的かということです。
また、問題事象が現在進行形で発生中である場合といったん沈静化しているが、将来
に向けて何らかの知見を得て組織の技術資産としたい場合とでは、対応方法に違いが
ありますので、2つの場合に分けて考えていきます。
1)問題事象が現在発生中の場合
①どこで発生し、どこで見逃し、どこで拡大しているかの調査結果から、
発生源>見逃し源>拡大源 の優先順位で対策立案する。
②発生源がわかっていても対策が難しいなら、結果への影響を極小化するよう考慮する。
③問題の被害者などが存在すれば、その対応を迅速、的確、誠実に実施する。
2)将来へ向けて対応したい場合
①原因構造解明で明らかにした問題発生メカニズムの全貌を考察して、どの因果連鎖を
どう断ち切るか、どう軟着陸させるように誘導するか、広い視野から検討します。
候補となりうる対策を広い視野から吟味することが大切です。
②どのような対応を取るか考察する際には、候補となっている対応策について
効果、経済性、(技術的)実現可能性、対応策実施の完全性・継続性、対応策の
副次的効果などについて検討します。
(6)ステップ6:対策実施
対策実施は、ステップ5で立案された実行計画に基づいて実施します。
実施にあたって注意することは、
①関係者と十分な連携を図る
・新しいことに取り組むと、良いことだとはわかっていても変えたくない人からの
反発や抵抗があり得ますので、きちんと納得するまで説明することが大切です。
・対策の節目で関係部署に「報連相」をすることが円滑に進めるコツです。
「報連相のポイント」
Why(目的・狙い)・・・何のために
What(課題)・・・何をどの程度
Where(対象範囲)・・・どこを対象に
How(手段)・・・どのようにして
When(時期)・・・いつまでに
Who(体制)・・・誰が
How much(費用)・・・いくらかかる
②テストを行いながら実施する
対策の内容や規模にもよりますが、本対策の前にテスト(トライ)をして対策の
確かさを確認してから、本対策を実施します。
③データを取りながら実施する
対策途中で予想外の結果が出たときに、それまでのデータを解析することによって
計画を修正することも可能になるため、できるだけ因果のデータを取るようにします。
また、最後に結果を評価する場合にもデータが必要になります。
(7)ステップ7:効果確認・評価
評価は、対策の結果、目的が達成できたかどうかで最終判断します。
①目標は達成できたか、あるべき姿が実現できたか
②目的は達成できたか
③予期しない弊害項目が発生しなかったか
④マイナス効果が出てなかったか
⑤技術資産、知的資産として獲得できたものを整理する
(8)ステップ8:標準化
標準化とは、二度と同じ問題が起こらないように再発防止、未然防止をすることです。
標準化のポイントは
①仕事のやり方、仕組みを変え、それを形式知化して残す。
②標準化した内容を関係者に周知させ、一人ひとりが実施可能になる教育訓練の
仕組みも残す
③その標準化の意味を理解し、組織風土として定着させる仕掛けをする
3. まとめ
トヨタ流問題解決の特徴は何かというと、「お客様第一」、「全員参加」、「絶え間ない改善」
というTQMの3本柱と「知恵と改善」、「人間性尊重」というトヨタのDNAともいうべきトヨタウェイ
2001であろうと思います。
そして、この問題解決の8ステップはトヨタビジネスプラクティス(TBP)と呼ばれ、全社員が
共有できるように、新入社員教育から始まり、階層別教育にも織り込まれ、「これが標準語
であり、共通語だ」と言われるほど徹底して繰り返し実践されていきます。
そうすることによって、個人の問題解決活動を組織の記憶として定着させ、それを他部門
にも展開していくということが日常業務に完全に組込まれているのです。
その結果、個人の技術、知識を組織としての技術資産、知識資産として蓄積、共有すること
によって、組織能力向上につなげているということなのです。
こうしたことを愚直に粛々と実行し続けられるところに確固たる強みを感じます。
今回は関連のある3つの記事で、トヨタ流問題解決の秘訣を解説しています。
是非これらの記事も御覧ください。
関連記事はこちらをクリックしてください!
===>トヨタ流問題解決「A3仕事術」の誰も知らない本当の狙い
よろしくお願いします。
【参考文献】
1)飯塚悦功、金子龍三(2012):「原因分析〜構造モデルベース分析術〜」
日科技連出版社